Click here to view and download our catalogue Our Solutions and Processes for the Feed-Milling and Material Handling Industries"Grain Tech has an extensive range of bulk materials and handling equipment to meet your needs!"
We are old hands in the materials handling field and will design handling systems to meet your needs. From a few pounds per hour to hundreds of tonne per hour Grain Tech has a solution with a commitment to superior performance at an economical investment. Apart from the well-known drag link conveyors, screw conveyors and bucket elevators we have unique handling equipment such as rotary metering feeders, volumetric blenders, bin activators and multi-way diverter valves. Installation arrangements are detailed using the latest CAD design software operated by experienced engineers.
The image below illustrates what we can provide for your business.
|
![]() |
![]() |
![]() |
Drag Chain Conveyors
- Standard design series.
- Available in capacity sizes from 30 m³/hr through to
1600 m³/hr.
- Heavy Duty folded and flange fitted design with bolt
together fabrication.
- Fitted with high tensile chain and UHMW Polyethylene conveyor flighting for stable, low noise running and long service life.
- Multi point feeding and discharge to suit installation
requirements.
- Incorporates heavy duty gear drive arrangement
and chain adjustment mechanism - Equipped with safety over flow alarm
Z Pattern Bucket Elevators
- Available in capacities from 6.5 MTPH – 25 MTPH in six
sizes.
- Suited for incorporation into transfer applications where
gentle handling is necessary such as seed and grain varieties,
rice grain, specialty grain handling applications as well as
finished product handling where non-degradation is required.
- Head and boot assemblies and leg sections are designed
and fabricated to provide optimum sealing and strength.
- Dual inlet assemblies to meet process requirements.
![]() |
![]() |
![]() |
Super Flo Drag Link Conveyors
- Available in capacities from 6.5 MTPH –
25 MTPH in six sizes.
- Suited for incorporation into transfer applications
where gentle handling is necessary such as seed
and grain varieties, rice grain, specialty grain
handling applications as well as finished product handling
where non-degradation is required. - Head and boot assemblies and leg sections are designed
and fabricated to provide optimum sealing and strength.
- Dual inlet assemblies to meet process requirements.
Screw Conveyors
- Capacity sizes from 10 m³/hr. through to 320 m³/hr.
- Heavy duty fabrication with folded and flanged assembly
components.
- Cyclodrive gear unit c/w chain & sprocket transmission
- Installed with intermediate hanger bearings and heavy
duty flange mounted bearings for the shaft spindles.
- May be supplied with overflow safely cut out device
![]() |
![]() |
![]() |
Metering Screw Feeders
- Capacity sizes from 10 m3 / hr. through to 800 m3 / hr.
- Fitted with heavy duty variable pitched feed section
flighting.
- Heavy duty folded and flange fitted design with bolt
together fabrication and assembly.
- Optional direct drive or chain and sprocket transmission
from a cyclo-drive gear unit.
Twin Screw Feeders
- Capacity sizes from 20 m3 / hr. through to 800 m3 / hr.
- Incorporates variable pitch flighting for the infeed section.
- Fitted with flange mounted bearing sets complete with seals.
- Optional direct drive or chain and sprocket transmission from
cyclo-drive gear unit.
- Suited for high capacity metering feeding and batching
applications.
Rotary Dischargers
- Capacity sizes from 5 m³/hr. through to 500 m³/hr.
- Suited for metering feed discharge into weigh hoppers
and regulating material supply to processing applications. - May be supplies with either a single or a dual discharge
outlet.
- Heavy duty fabrication with welded and flanges bolt
together assembly.
- Rotor is driven from a cyclo-drive gear unit c/w V/S
control.
Bin Vibratory Dischargers
![]() |
- Proven worldwide to give continuous but controlled flow of difficult to handle materials from bulk storage silos and bins through the controlled use of vibration.
- Eliminates possibility of ratholing, degradation and segregation of materials within the silo to ensure an even flow of material on a mass flow basis.
- May be arranged with single or multiple discharge outlets.
- Supplied as a pre-assembled unit ready to be bolted upto the silo or bin.
- Ideal for regulated feeding to metering feed conveyors, rotary valves, weigh belt feeders, transfer conveyors and delivery to bulk tankers.
- Available in a range to sizes and capacities from 600 mm ø – 3000 mm ø.
- May be supplied in painted carbon steel and stainless steel fabrication.
![]() |
![]() |
![]() |
![]() |
Rotary Distributors
- Capacity sizes from 10 m3 / hr. through to 70 MTPH.
- Suited to alternative spout sizes for 200 mm, 250 mm, 300 mm and 320 mm diameter.
- Available with optional 4, 6, 8, 10, 12, 14 or 16 outlet from single inlet.
- Heavy duty fabrication incorporating welded and flange fit bolt together components.
- Convenient for simplifying bulk material multi-distribution transfer.
|
|
|
Bulk Storage Silos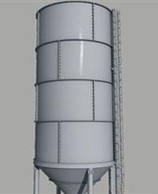
- Bolt together panel design suited for on-site assembly.
- Capacities from 10 m3 through to 450 m3
- Available with conical round outlet discharge or flanged
hopper to suit various metering feed dischargers.
- Fabrication is from heavy gauge carbon steel flanged
panels designed for sealant and site blot together
assembly complete with bolt together roof panel assembly
and flanged conical hopper. The silo hip is fitted with heavy
duty gusseted leg mounting assemblies suited to fitting the
round section leg supports complete with bracing members.
High tensile bolts in two rows are used to secure the panels
on assembly. A top center inlet spigot is fitted and level
sensor flanged cut outs are provided. OSH compliant hand
railing, kick plates and access ladder complete with man
protective cage is allowed for.
To meet the requirements for bulk handling, Grain Tech provides bolt together galvanized hopper bottom silos ranging from 3.5 to 22 meters in diameter and capacities of 5 - 5000 metric tons.
|
|
These silos may be elevated for bulk transport loading. Dust free discharge chutes may be fitted to bulk out loading silos to maintain clean transfer and out loading operations.
|
![]() |
Slide Gate Valves
- Available in a wide range of sizes to suit different spouting
requirements from 200 mm x 200 mm through to
800 mm x 800 mm and capacities from 50 m³/hr. through to 800 m³/hr.
- Heavy duty design with welded and bolt together fabrication
- Available with either pneumatic, electro-serve or manual activation
- Easily installed with low maintenance and reliable operation
![]() |
![]() |
![]() |
![]() |
Diverter Valves
- Available in sizes from 200 mm x 200 mm through to
800 mm x 800 mm and capacities from 50 m³/hr. through to
800 m³/hr. with 30° and 45° discharge angle.
- Welded and flange fit fabrication with heavy duty flap
assembly.
- Available with pneumatic or electro-serve activation.
- May be supplied with optional discharge configuration
![]() |
![]() |
![]() |
Air Cushion Conveyors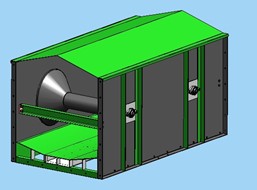
- Capacity sizes up to 2500 m3 / hr.
- Suited for long distance conveying applications
- Smooth and reliable operation with consistent
belt tracking
- May be run in either direction and arranged to
discharge at either end or centre point according to installation
requirements.
- Incorporates self-cleaning features and safety features
including alignment sensing, pressure sensor, speed monitoring
and choke sensing.
- Suited for incorporation into a wide range of conveying
applications where high capacity operation at a lower operating
cost is called for.
![]() |
![]() |
Magnetic Separators
- Capacity sizes from 10 MTPH to 100 MTPH
- Five different sizes.
- Rare earth bulb design installed up to a swing away door for ease of cleaning.
- Magnetic field intensity = ≥ 3000 GS
- Iron removal efficiency = ≥ 99%
- Available with either stainless steel or optional carbon steel casing assembly.
Special Application Bucket Elevators
![]() |
![]() |
These bucket elevators are designed for gently handling seeds, grain, oilseeds,
pulses and similar products where degradation of the seed
and damage to the germination quality of the material
is to be avoided. The bucket elevators are also ideal for
incorporation within the rice milling, maize milling,
rice drying, maize drying and similar cereal grain
and seed processing applications where attritional product
damage is to be minimized and where cross-contamination
is prohibited.
The main features of these bucket elevators are:
- Special design elevator head section for lower linear velocity product discharge while avoiding backflow of product down the return leg.
- Flanged double-entry fittings to the elevator boot section designed for gentle product entry and minimum deflection.
- Rubber bonded head pulley and squirrel cage type tail pulley for optimum friction between the elevator belt and pulley drives.
- Easily removed boot cleanout slide panel to enable complete cleanout from one line to another.
- Large section removable inspection door fitted to the up-leg section to enable the easy inspection and wiping out of buckets where required.
- Heavy-duty fabrication with sealed flanges for all
elevator assemblies.
- Controlled metering to either of the down leg or up leg
boot section for versatile planning-in to the process
arrangement.
- Finish is in a top enamel coat over a rust-resistant
undercoat onto a prepared metal surface.
Pneumatic Conveying
- Dedicated to providing competitive solid materials pneumatic handling solutions and services.
- Positive dilute phase pressure conveying.
- Negative dilute phase vacuum conveying.
- Dense phase pressure pneumatic conveying
- Bulk material unpacking conveying systems
- Automatic ingredient metering + weighing systems
- Capacities from a few hundred kg through to 30MT per hour
- Complete range of pneumatic conveying equipment to suit new and retro fit installation applications
![]() |
![]() |
Intake receiving conveyor (from pit)
Grain Tech can manufacture and supply suitable conveyors for drive over pit truck discharge. The system comes complete with:
- Shallow profile hopper fabricated from carbon steel
- Top drive over grid suitable for discharged ingredients to flow through complete with heavy-duty support members capable of supporting loaded truck and trailer units.
- En-masse drag link design pick up conveyor
- Horizontal in-feed with inclination for discharge into the following bucket elevator
- Fabricated from heavy-duty carbon steel folded and welded casing suited for bolt-together assembly. High tension conveying chain fitted with UHMW flighting.
![]() |
|
|
|
Disc and Tube Conveyors
The tube chain conveyor is designed to continuously convey
fine powder granules and bulk materials. It can be installed as
horizontal and vertical and standalone vertical arrangement
Delivery capacity: 0.4-300m3/h according to model & size
Max. Delivery Distance: 80m (horizontal); 60m (vertical)
Power: 0.2-30KW according to model & size
Tube Chain Conveyor System's Feature:
- Sealed Pattern: dust-tight
- Low Energy Consumption
- No dead areas
- No metal on metal friction
- Low maintenance cost
- Long life time operation
- Explosion and pressure shock resistant design
- Possible to re-start in filled state
- Minimal grain or material degradation
Possible configurations:
Pneumatic Conveying Units
The vacuum conveyor is designed for industrial applications incorporating heavy-duty components and is the ideal transfer equipment, used for transporting powder and granular materials for feeding the materials directly into mixers, sifters and other processing equipment. It reduces the likely dust emissions and is GMP certified. It is widely used in the pharmaceutical, foodstuff, feedstuff, chemical and plastics industries and for general processing material handling applications. The capacity range is from 0.4-6 metric ton per hour.
Working Principle:
The vacuum conveyor consists of a vacuum unit (no oil, no water), feeding tube, PE filter, vacuum hopper, automatic control device, pneumatic discharging device and a compressed air pulsing unit.
The ZKS conveying units have the characteristics of low power consumption high capacity, low noise and reliable operation. It is the ideal type of equipment for transferring powder and granular materials to mixers and processing equipment including sifters, packers, reactors etc.
Note:
-Pneumatic receiver to be placed above hopper.
-Vacuum unit on the floor beside hopper
Integrated Control Systems
For reliable and efficient plant operation, GTE provides complete package Integrated Control Systems incorporating all necessary contactors, starters, overloads, mains switches, housed within easy accessed MCC units. PLC operational units complete with PC's and monitors together with custom software complete the pre-wired package ready for field wiring to the equipment items on site. This Integrated Control System arrangement enables greater installation economics and a significant saving in installation time requirements.
|
|
|
|
Engineering Services
Over the past twenty-four years, we have completed projects throughout Australasia offering a total capability of design, project management, equipment supply, installation and commissioning within the bulk materials handling and associated cereals processing industries.
This approach has enabled customers to make the most cost-effective use of their resources according to individual specifications. Using our most up-to-date techniques and design software, we can meet your requirements.
The following images are a sample of the projects we have previously undertaken.
|
|
|